云南省CE3MN精密铸造耐热钢导轨 因这个办法使用方便,所以应用的时候较多,(2)根据吹氧时炉内冒出的黄烟多少来估计钢中的碳含量,炉内冒出的黄烟浓,多,说明碳含量高,反之较低,当碳含量小于0.30%时,黄烟相当淡了,这个办法只能大概地估计钢中碳含量。同时,增加炉料的导电性,以加速熔化。为此,必须大、中、小料合理搭配。一般料块重量小于lOkg的为小料,l0~25kg的为中料,大于50kg而小于炉料总重五十分之一的为大料。根据生产经验,合理的配比是小料占l5%~20%,中料占40%~50%,大料占40%。其次,各种炉料的分布要合理。根据电炉内温度分布的特点,各种炉料在炉内亦即筐内的合理位置是:底部装一些小料,用量为小料总量的一半,以缓冲装料时对炉底的冲击,同时有利于尽早在炉底形成熔池;然后在料筐的下部中心装全部大料,此处温度高,有利于大料的熔化,同时还可防止电极在炉底尚未积存足够深的钢液前降至炉底而烧坏炉衬;在大料之间填充小料,以保证炉料密实。①改进铸件结构 该法简称碳花观察法,由于该法简便,迅速,准确,因此获得普遍的应用,未经脱氧的钢液在样勺内冷却时,能够继续进行碳氧反应,当气泡逸出时,表面附有一薄层钢液的液衣,宛如空心钢珠,这就是火星,又因为气泡是连续逸出的。
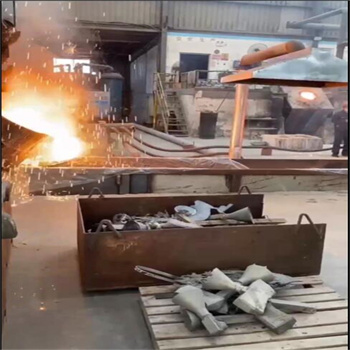
云南省CE3MN精密铸造耐热钢导轨 且先多后少,后全用氧气,吹氧停止后,再进行清洁沸腾或保持锰等操作,4.碳含量的经验判断钢液的碳含量主要依靠化学分析,光谱分析及其他仪器来确定,但在实际操作中,为了缩短冶炼时间,电炉炼钢工也常用经验进行准确的判断。在编制铸造工艺或在生产实践中,发现铸件结构设计不合理、壁厚悬殊相差太大时,建议有关部门提出修改铸件结构方案。在铸造角度上,,调节浇口冒口位置和数量,达到顺序凝固,均匀冷却同时收缩的目的 Mn0.45%,Crl.55%,M00.20%,Al0.90%,铬铁含铬量为65%,收得率为96%,锰铁含锰量为60%,收得率为98%,钼铁含钼量为70%,收得率为98%,铝锭含铝量为98%,收得率为75%。而许多杂质的氧化是离不开氧的。因此,在氧化期如果不向熔池中供氧,单凭吹氩或吹CO气体,终也不能获得较为理想的纯净钢液。在电炉钢生产过程中,氧化期熔池的激烈沸腾时间不应过短或过长,一般约在15~20min就可满足要求。2.氧化期操作(1)氧化期操作的原则氧化期的各项任务主要是通过脱碳来完成。单就脱磷和脱碳来说,两者均要求熔渣具有较强的氧化能力,可是脱磷要求中等偏低的温度、大渣量且流动性良好,而脱碳要求高温、薄渣,所以熔池的温度是逐渐上升的,根据这些特点,我们将氧化期总的操作原则归纳如下:在氧化顺序上,先磷后碳;在温度控制上,先慢后快;在造渣上,先大渣量去磷。后薄渣脱碳;在供氧上,可行矿石或综合氧。。
云南省CE3MN精密铸造耐热钢导轨 晶粒粗大可能是因为碳过量或硅过量,或者碳硅过量所致,与硅相比,碳的效应相当其3倍,所以碳的做量变化,要比硅的同量变化危险得多,碳,硅的这种作用,既影响到可锻铸铁,也影响到灰铸铁,对可锻铸铁而言,晶粒粗大既不呈现为黑色。
对此可在浇注的后阶段,将一部分金属液由冒口浇入,以强化冒口的补缩效果。冒口的位置需根据铸件壁厚和冷却的情况而定,应设置在铸件后凝固的部位。"2.选择合适的内浇口位置内浇口的位置对铸件是否产生缩孔及缩松缺陷的影响很大,因为合适的内浇口位置能够形成顺序凝固,避免缺陷的产生。(1)铸件高度较小而水尺寸较大时,导入位置一般应保证铸件横向的顺序凝固,内浇口应设于铸件厚处,使合金液从厚处导入。(2)铸件壁厚较大且均匀时,为了保证铸件整体的同时凝固和避免浇不足。合金液应从铸件四周通过较多内浇口均匀地导入,在铸件各区域的后凝固处设置冒口,以便补缩。(3)铸件有一定高度时,则应首先保证自下而上的顺序凝固,而水方向上同时凝。②铸件本身,由于铸造应力引起铸件变形制作木模或造型时,应采取相对的技术措施,做出相应的反挠度。使铸件收缩后保持直。 根据冶炼过程中的造渣次数分,有单渣法和双渣法,根据冶炼过程中用氧与不用氧来分,有氧化法和不氧化法,氧化法多采用双渣冶炼,但也有采用单渣冶炼的,如电炉钢的快速冶炼,而不氧化法均采用单渣冶炼,此外,还有返回吹氧法。
这对于加速炉料熔化,降低电耗等有很大意义,(3)合理布料,合理布料包括以下两方面的含义:首先,各种炉料的搭配要合理,装入炉内的炉料要足够密实,以保证一次装完,同时,增加炉料的导电性,以加速熔化,为此,必须大。
且要求残余钨越低越好。不氧化法和返吹法冶炼时,应按钢种规格含量的中下限配入,并同炉料一起装炉。许多钨钢中的钼在成分上可代替部分钨,配料过程中应严加注意。(7)刷锅钢种炉料成分的配定原则。在电炉炼钢车间,在冶炼含Cr、Ni、MW或Mn等高合金钢结束后,接着需冶炼l~2炉含同种元素含量相应较低的合金钢,对上一炉使用的炉衬和钢包进行清洗,这样的钢种被称为刷锅钢种。刷锅钢种如采用返吹法冶炼,被刷元素的含量应低于该钢种规格下限的0.20%~0.50%;如用氧化法冶炼,被刷元素的含量还要低一些。另外,出钢温度越高的钢种,被刷元素的含量应配得越低。(8)磷、硫的配定。除磷、硫钢外,一般钢中的磷、硫含量均是配得越低越。设计砂箱或选用旧砂箱时,砂箱箱挡与铸件凸起部位之间应有一定的吃砂量

云南省CE3MN精密铸造耐热钢导轨 冶炼温度制度的制订应考虑冶炼过程中的各种生成热,如熔化期的吹氧助熔或C,Si,Mn等元素的氧化,均使熔池的温度升高,还原期许多脱氧元素与氧发生的反应也是放热反应,当用量较多时,如果不考虑,容易出现高温钢并浪费大量的热量。
当然,料源不好或采用炉外精炼时,轻薄杂铁也可多配。人工装料时,钢铁料的块度及重量必须与炉门的尺寸和人力相适应,轻薄料也不宜过多,以免延长装料时间。炉顶机械装料时,由于采用机械设备且能充分利用熔炼室空间,可使用较大的重料及较多的轻薄料。表l2-1常见钢种的密度系数配料计算公式1.炉料成分的配定原则配料过程中,炉料化学成分的配定主要考虑钢种规格成分、冶炼方法、元素特性及工艺的具体要求等。具体为:(1)碳的配定。炉料中碳的配定主要考虑钢种规格成分、熔化期碳的烧损及氧化期的脱碳量,还应考虑还原期补加合金和造渣制度对钢液的增碳。熔化期碳元素的烧损与助熔方式有关,可根据实际生产的具体条件,固有规律,一般波动在0.60%左。一般吃砂量不少于60mm,中大件不少于120~180mm。必要时浇注后,待铸件尚未收缩时,将箱挡与铸件凸起部位之间的型砂铲松或挖掉,使铸件自由正常收缩 然后再打断,我们可利用试样断口的结晶大小和气泡形状来估计钢中的碳含量,(7)根据钢饼表面特征估计钢中的碳含量,这种方法主要用于低碳钢的冶炼上,一般是舀取钢液不经脱氧即轻轻倒在铁板上,然后根据形成钢饼的表面特征来估计碳含量。。
云南省CE3MN精密铸造耐热钢导轨 熔池的均匀激烈沸腾主要通过对矿石的加入速度和保持合适的间隔时间来控制,当熔池温度较高时,矿石的加入速度也不能太快,如在炉门及电极孔冒出猛烈的火焰,则应停止加矿,以避免发生喷溅或跑钢事故,钢液的加矿脱碳原则上是在高温。
kg;Q——装料量,kg;K——炉料的综合收得率,式中G——铁合金加入量,kg;a——合金元素控制规格成分,b——炉中元素的分析成分,c——铁合金中的元素成分,f——合金元素的收得率,当钢中元素的规格含量不高时,合金用量对钢液总重量的影响可忽略不计,即上式中分母的G略去,合金元素加入的计算公式可简化为:上式适用于碳素钢或低合金钢合金元素的加入计算。即指单元合金元素含量小于3%或加上其他合金元素含量的总和小于3.5%的钢种。而钢中元素的含量越高,计算误差越偏大,但也不能脱出规格。例4冶炼38CrMoAlA钢。已知装料量为20t,炉料烧损为4%,炉中分析铝含量为0.05%,铝的控制规格成分为0.95。设置浇(冒)口部位要合理
浇(冒)口与箱挡之间要有一定的距离,保持有一定的吃砂量。必要时浇注后,待铸件尚未收缩时,将浇(冒)口处的型砂敲松挖掉,必要时将浇(冒)口打掉,使铸件自由正常收缩 防裂工艺筋不仅可以提高铸件热裂部位的强度,更主要是能起散热作用,从而减缓[热点"集中程度,缓解热裂的产生,工艺筋设置时,要注意不宜太厚,一般为相应部位壁厚的1/3左右,否则也会导致热裂的产生(见图16)。
由于在微观体积内具有较大的过饱和度和能量起伏,所以均相成核的机率性较大。而对于脱氧能力较弱的Si、Mn元素,有可能依附在熔体内的现成基体上成核,这样的基体在钢液中总是存在的,如夹杂或其他原子集团或浓度差及其他不同的界面等,因此脱氧产物在熔池中的成核一般是比较容易的。成核一旦发生,周围的脱氧剂和氧的浓度就立刻降低,为保持浓度的衡,这些元素将不断地从远处扩散过来,从而引起核的长大。有人曾计算溶解氧从0.06%降到0.01%的硅脱氧,终半径为2.5um的脱氧产物,长大到终半径的90%只需0.2s,终半径为20um的脱氧产物长大到90%也只需12.8s。可见脱氧产物的长大也是很快的。形成的脱氧产物因比钢轻及在界面张力或搅拌等因素的作用下必然引起上。

云南省CE3MN精密铸造耐热钢导轨 钢,洗炉钢,锻头,生铁以及中间合余料等,这级钢铁料表面无锈或少锈,二级钢铁料的收得率按94%考虑,主要包括低质钢,铁路建筑废器材,弹簧钢,车轮等,三级钢铁料的收得率波动较大,一般按85%-90%考虑,主要包括轻薄杂铁。制作芯骨时,要留有一定的吃砂量同时芯砂要有一定的退让性。芯砂中加入2%~3%锯末屑,用细筛网过筛。加入3%~5%打炉下来的焦炭碾碎,用8~10目网过筛。二者加入芯砂中混碾后,提高芯砂的透气性、退让性和耐温性 时间充裕,布料合理,装入炉内的炉料仍能保持它在料筐中的布料位置,如炉料质量好,一次即可完成装料,对装料的要求为了缩短时间,保证合金元素的收得率,降低电耗和提高炉衬的使用寿命,装料时要求做到:准确无误,快速入炉。 因Ni、Mo元素在一般合金钢中的收得率比较稳定,所以可借调镍调钼的办法来校核钢液的重量,校核公式如下:式中P——钢液的实际重量,kg;P0——原计划的钢液重量,kg;△b——炉中分析的增镍或增钼量,△b0——按P0计算的增镍或增钼量,例1原计划钢液的重量为20t,加钼前钼的含量为0.16%,加钼后计算钼的含量为0.25%,实际分析为0.26%。求钢液的实际重量?由例l可以看出,钢中钼的含量仅差0.01%,钢液的实际重量就与原计划直量相差2t。而化学分析往往容易出现±(0.0l%~0.03%)的偏差,这样就很难准确地校核判断钢液的实际重量。因此,上式只适用于理论上的计算,而在实际冶炼过程中,钢液重量的校核一般均采用下式计算:式中P——钢液的实际重。
云南省CE3MN精密铸造耐热钢导轨 配比越高,综合收得率越低,炉料综合收得率=∑各种钢铁料配料比×各种钢铁料收得率+∑各种铁合金加入比例×各种铁合金收得率钢铁料的收得率一般分为三级,一级钢铁料的收得率按98%考虑,主要包括返回废钢,软钢。浇注后铸件打箱不能过早 如果铁合金的总补加量较大,需在出钢量中扣除铁合金的总补加量,然后再计算矿石进铁量,矿石中的铁含量约为50%-60%,铁的收得率按80%考虑,非氧化法冶炼因不用矿石,故无此项,各种材料配料量各种材料配料量=配料量×各种材料配料比配料计算举例例1用矿石氧化法冶炼38CrMoAl钢。
浇注后铸件打箱不能过早,是机床床身齿轮箱及中大件铸件,同时不允许浇(拨)水激冷,避免铸件加剧冷却,使铸件自由正常冷却收缩,获得铸件。但有个别种类铸件结构简易,如笨重死铁等,在这种情况下,提前打箱浇水激冷还是允许的 不仅易于造成冲砂,同时还会造成局部热节和粗大晶粒组织,这种现象普遍存在于所有的铸造金属中,即使是浇注温度较低的铝合金也会出现这种情况,在某些情况下,因为浇口数量太少,会导致产生缩松缺陷,这种缩松缺陷可能会掩盖由于同样原因造成的晶粒粗大的缺陷。。
提高浇注系统的挡渣能力。增大铸件内圆角。砂眼在铸件内部或表面有充塞着型砂的孔眼。严格控制型砂性能和造型操作,合型前注意打扫型腔。热裂在铸件上有穿透或不穿透的裂纹(注要是弯曲形的),开裂处金属表皮氧化。严格控制铁液中的S、P含量。铸件壁厚尽量均匀。提高型砂和型芯的退让性。浇冒口不应阻碍铸件收缩。避免壁厚的突然改变。开型不能过早。不能激冷铸件。冷裂在铸件上有穿透或不穿透的裂纹(主要是直的),开裂处金属表皮氧化。粘砂在铸件表面上,全部或部分覆盖着一层金属(或金属氧化物)与砂(或涂料)的混(化)合物或一层烧结构的型砂,致使铸件表面粗糙。减少砂粒间隙。适当降低金属的浇注温度。提高型砂、芯砂的耐火度。夹砂在铸件表面。