湖南省ZG3Cr18Mn12Si2N高铬铸件炉底板 根据氧化期供氧方式的不同,有矿石氧化法,氧气氧化法和矿,氧综合氧化法及氩氧混吹法,冶炼方法的确定主要取决于炉料的组成以及对成品钢的质量要求,下面我们扼要介绍几种冶炼方法:(1)氧化法,氧化法冶炼的特点是有氧化期。铸件结构设计不合理,往往是热裂产生的原因之一。所以,在设计铸件时应注意以下几点:a、两截而相交处不要设计成直角拐弯,须设有圆角。圆角的形状、大小视铸件的交接情况确定。图7举例说明同一用途的两种铸钢件结构。图7(a)所示结构由于两截面交接成一直角拐弯,形成了热节,造成收缩应力易于此处集中和热裂的形成。若改为图7(b)所示圆弧形结构后,热裂即被消除。图片b、尽量减小并分散热节点,避免采用十字交叉的截面,在条件允许的情况下,应将交叉的截面错开。图10是各种连接形式的合理与不合理结构的对比实例。图片图片图片c、必须在钢件上采用不等厚度的截面时,应使铸件各部分收缩时彼此不发生阻碍。例如手轮、齿轮等轮类铸件除在转角处做出圆角。①改进铸件结构 修正浇注系统设计,使温度低的金属熔液位于铸件截面较厚的部位,并在铸件的厚截面处设计有效的冒口,以尽可能减小冒口的尺寸,(2)对于带孔铸件,工艺设计人员有时没有采用有助于减小有效截面尺寸的型芯,使未设芯的截面过厚而产生此缺陷。
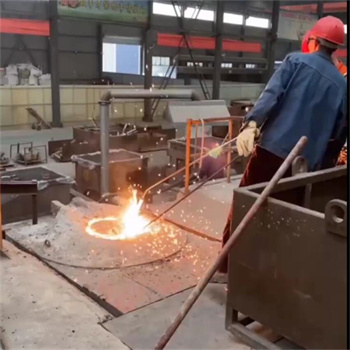
湖南省ZG3Cr18Mn12Si2N高铬铸件炉底板 目前,广泛采用的还是料筐顶装料,其装料过程是:将炉料按一定要求装在用铁链销住底部的料筐中,装料时,先抬起炉盖,并将其旋转到炉子的后侧或将炉体开出,然后再用天车将料筐从炉顶吊入炉内,而后拉开销子卸料入炉。在编制铸造工艺或在生产实践中,发现铸件结构设计不合理、壁厚悬殊相差太大时,建议有关部门提出修改铸件结构方案。在铸造角度上,,调节浇口冒口位置和数量,达到顺序凝固,均匀冷却同时收缩的目的 根据冶炼方法的不同特点使用钢铁料,钢铁料的化学成分必须符合冶炼钢种的需要,氧化法有较好的脱磷,去气,除夹杂的能力,应多使用普通的粗料,返吹法和不氧化法因脱磷,去气,除夹杂能力不强,但能回收贵重的合金元素。然后再调入少量炭粉使炉内保持正压进行脱氧,同样能得到相同的效果。碳化钙在渣中既能溶解又能扩散,脱氧反应如下:在碳化钙进行脱氧的同时,为了保持正压而使用的炭粉在较低的温度区域内也能还原渣中的(FeO)和(MnO)。电石渣是高碱性的还原熔渣,脱氧能力比白渣强。为使钢液充分脱氧,电石渣应保持20~30min。在电石渣下操作,除温度不好控制外,钢液还易增硅,大约增硅0.05%~0.15%/h,这是由于CaC2与渣中(SiO2)发生反应的结果。反应式如下:此外,还易使钢液增碳,每小时约增碳0.05%~0.10%。如果采用电石渣出钢,渣中的游离碳也会使钢的成品碳。电石渣因碳化钙含量不同分为弱电石渣(CaC21%~1.5%)和强电石渣(CaC22%~4%。。
湖南省ZG3Cr18Mn12Si2N高铬铸件炉底板 至于低沸点的Zn,Pb等就更容易挥发了,间接挥发是通过元素的氧化物进行的,即先形成氧化物,然后氧化物在高温下挥发逸出,一般说来,多数金属氧化物的沸点低于该金属的沸点,如M0的沸点为4800℃,而M003。
尤其是出钢后的喷粉操作,在进行脱氧、脱硫的同时,还可降低脱氧产物SiO2等的活度,更有助于它们的排除。总之,钢中脱氧产物的排除程度,在冶炼过程中取决于脱氧产物的组成和性质,这与脱氧工艺有直接关系。脱氧产物的颗粒越大,或密度差越大,或熔点低呈液态并与钢液间的界面张力越大,排除程度越好。此外,控制合适的冶炼温度及加强不同形式的搅拌,也有利于脱氧产物的上浮与排除。2.电炉炼钢的脱氧方法1)直接脱氧直接脱氧就是脱氧剂与钢液直接作用,它又分为沉淀脱氧和喷粉脱氧两种。扒净氧化渣后,迅速将块状脱氧剂。如锰铁、硅锰合金或铝块(饼)或其他多元素的脱氧剂,直接投入(插入)钢中或加到钢液的镜面上,然后造还原稀薄渣,这种脱氧方法称为钢液的沉淀脱。②铸件本身,由于铸造应力引起铸件变形制作木模或造型时,应采取相对的技术措施,做出相应的反挠度。使铸件收缩后保持直。 吹氧脱碳冶炼时间短,可提高产量20%以上,电耗降低l5%-30%,电极消耗降低l5%-30%,总成本约降低6%-8%,且钢的质量也大有改善,吹氧降碳时,好选用较高的氧压,因为氧压高,氧气流在钢液内可吹入到更深的部位。
此外,在制订冶炼温度制度时,还应考虑冶炼过程中的各种温度降,如氧化末期的全扒渣降温,造渣材料和各种铁合金从常温加热到熔点,再由固态转变为液态的吸热降温,中间出钢法的降温,出钢过程及包中精炼或采用固体合成渣的降温。
化学分析能够快速测出还原渣中(FeO)的含量。如果渣中(FeO)的含量小于0.5%,表明钢液的脱氧较好。(4)仪表测量法。目前,通过仪表可直接测出钢液中的氧含量。所用的仪表有快速定氧定碳仪、电子电位差计、浓差电池定氧仪,还有测温定氧仪等多种。这些仪表使用方便,快速准确,有的只需几秒钟就可确切知道钢中的氧含量。因此,已在许多炼钢单位得到了普遍的应用。5.钢液的终脱氧为了进一步降低钢中氧含量,根据工艺要求,在出钢前或往出钢槽、出钢流中,也可在钢包中或在浇注过程中加入脱氧能力更强的元素,即在凝固前对钢液进行后一次直接脱氧,称为钢液的终脱氧。经过终脱氧的钢液,凝固后可获得理想的结晶组织,各种性能也得到了提。设计砂箱或选用旧砂箱时,砂箱箱挡与铸件凸起部位之间应有一定的吃砂量

湖南省ZG3Cr18Mn12Si2N高铬铸件炉底板 各元素氧化的动力学条件好,在供氧强度较高的情况下,更有利于低碳钢或超低碳钢的冶炼,氧气氧化属于放热反应,进而也有利于提高和均匀熔池温度而减少电能消耗,此外,氧气氧化后,钢液纯洁,带进其他杂质少,且吹氧后。
对于不同的铸造金属,必须采取小同的熔化工艺。(1)冲天炉熔化灰铸铁鼓风量和焦炭不衡,会造成过量增碳。例如,底焦高度过高和降低鼓风量会造成过量增碳。当炉衬熔蚀后,增碳会更加严重。因为冲天炉直径变大后,为了保持同样的含碳量,需增加鼓风量。在过高的温度下熔化会增加碳量,如果采用热风熔炼,就会遇到这种情况。根据经验,鼓风温度每增加55℃,就会增加0.10%的碳(质量分数)。如果采用氧气来提高温度,并不一定会产生同样的问题。出铁液的间隔过长,或铁液停留在炉缸中的时间过长,也会导致增碳。生产低碳铸铁一般都采用较浅的炉缸,并缩短出铁液的间隔时间,尽量做到连续出铁液。间断熔化会造成过量增碳,导致产生粗晶组织。另。一般吃砂量不少于60mm,中大件不少于120~180mm。必要时浇注后,待铸件尚未收缩时,将箱挡与铸件凸起部位之间的型砂铲松或挖掉,使铸件自由正常收缩 可在短时间内迅速提高钢液温度以及使钢液温度变得更加均匀,而还原期的熔池比较静,钢液中因合金元素与脱氧剂的引入,粘度增加,不利于分子的热振动或自由电子的穿过,另外,还原性钢液和氧化性钢液及还原渣和氧化渣的热导率不一样。。
湖南省ZG3Cr18Mn12Si2N高铬铸件炉底板 促使硫化物夹杂分布均匀,因而提高了铸钢的抗裂性,c,改进铸钢的脱氧工艺,能提高铸钢的抗裂性能,铸钢件晶界的氧化夹杂物是热裂形成的主要原因之一,提高脱氧效果,减少氧化夹杂物并改变其分布状态可以减少铸钢热裂倾向。
要立即迅速加入稀薄渣料,尽量减少钢液的吸气与降温。稀薄渣料中石灰和萤石的体积比为3.1,对于中等容量的炉子,渣料的加入量一般为钢水量的3%~3.5%,小炉子可取上限值。为使渣料快速熔化形成渣液覆盖钢液,应用较大的功率供电及推渣搅拌,直至形成流动性良好的熔渣。稀薄渣好一次造成,避免在还原过程中时而调稠、时而调稀,尽量做到造渣材料比及渣量准确,合理地使用电流电压等。根据工艺要求,薄渣料加入前或随同薄渣料一起加入块状脱氧剂进行预脱氧。其中,使钢中锰(包括钢中残余锰含量)达到(接)规格下限。硅达到0.10%~0.15%。薄渣形成后调入合金,然后按规程要求分批加入脱氧粉剂;批用量应多些,其他各批依次递减。设置浇(冒)口部位要合理
浇(冒)口与箱挡之间要有一定的距离,保持有一定的吃砂量。必要时浇注后,待铸件尚未收缩时,将浇(冒)口处的型砂敲松挖掉,必要时将浇(冒)口打掉,使铸件自由正常收缩 全熔后的硅不应大于0.30%,以免延缓熔池的沸腾时间,返吹法冶炼为了提高合金元素的收得率,根据工艺要求可配入硅废钢或硅铁,但也不宜超过1.0%以上,对于特殊情况也可不配,(3)锰的配定,用氧化法冶炼的钢种。
冷装主要使用固体钢铁料或海绵铁等。根据冶炼过程中的造渣次数分,有单渣法和双渣法。根据冶炼过程中用氧与不用氧来分,有氧化法和不氧化法。氧化法多采用双渣冶炼,但也有采用单渣冶炼的,如电炉钢的快速冶炼,而不氧化法均采用单渣冶炼。此外,还有返回吹氧法。根据氧化期供氧方式的不同,有矿石氧化法、氧气氧化法和矿、氧综合氧化法及氩氧混吹法。冶炼方法的确定主要取决于炉料的组成以及对成品钢的质量要求,下面我们扼要介绍几种冶炼方法:(1)氧化法。氧化法冶炼的特点是有氧化期,在冶炼过程中采用氧化剂用来氧化钢液中的Si、Mn、P等超规格的元素及其他杂质。因此,该法虽是采用粗料却能冶炼出高级钢,所以应用极为广泛。缺点是冶炼时间。

湖南省ZG3Cr18Mn12Si2N高铬铸件炉底板 如有接触要立即排除,以免送电后被击穿,如电极不够长时,好在送电前更换,以利于一次穿井成功,在冶炼低碳高合金钢时应注意电极的接尾或接头,如发现不牢固或有毛刺要打掉,避免冶炼过程中增碳,新换电极下端应无泥土或其他绝缘物质。制作芯骨时,要留有一定的吃砂量同时芯砂要有一定的退让性。芯砂中加入2%~3%锯末屑,用细筛网过筛。加入3%~5%打炉下来的焦炭碾碎,用8~10目网过筛。二者加入芯砂中混碾后,提高芯砂的透气性、退让性和耐温性 如去除钢液中的大部分磷和其他杂质以及减少或限制钢液的吸气与元素的挥发等,此外,有目的的升高熔池温度,为下一阶段冶炼的顺利进行创造条件,也是熔化期的另一重要任务,传统的电炉炼钢熔化期约占全炉冶炼时间的一半。 炉料的熔化过程大体上分a-起弧阶段;b-穿井阶段;c-电极回升阶段;d-低温区炉料熔化阶段阶段:起弧阶段。送电后,电极下降,当电极端部距炉料有一定的距离时,由于强大电流的作用,中间的空气被电离成离子,并放出大量的电子而形成导电的电弧,随之产生大量的光和热。起弧阶段的时间较短,约为3~5min,但常出现瞬时短路电流,所以电流一般不稳定并造成了对电网的冲击,从而产生了灯光闪烁或电视图像干扰等现象。第二阶段:穿井阶段。起弧后,在电弧的作用下,电极下的炉料首先熔化,随着炉料的熔化,电极逐渐下降并到达它的低位置,这就是穿井阶段。一般说来,极心圆较大的电炉往往在炉料部位,电极把炉料穿成比电极直径大30%~40%的三口小。
湖南省ZG3Cr18Mn12Si2N高铬铸件炉底板 脆性增加,这类缺陷多数是由于熔化操作不当所致,在铝合金中,是那些要求过热的铝合金,加入适量的细化品粒合金元素是必要的,(4)铜合金铜合金中晶粒粗大的缺陷常被针孔,气孔或缩松所掩盖,铜合金因成分变化会造成品粒粗大。浇注后铸件打箱不能过早 因这个办法使用方便,所以应用的时候较多,(2)根据吹氧时炉内冒出的黄烟多少来估计钢中的碳含量,炉内冒出的黄烟浓,多,说明碳含量高,反之较低,当碳含量小于0.30%时,黄烟相当淡了,这个办法只能大概地估计钢中碳含量。
浇注后铸件打箱不能过早,是机床床身齿轮箱及中大件铸件,同时不允许浇(拨)水激冷,避免铸件加剧冷却,使铸件自由正常冷却收缩,获得铸件。但有个别种类铸件结构简易,如笨重死铁等,在这种情况下,提前打箱浇水激冷还是允许的 C生为4.00%,C返为0.30%,C杂为0.10%,炉料综合收得率为96%,38CrMoAl的相对密度系数为0.9872,矿石的铁含量为60%,当配碳量为0.80%时,求配料量和配料组成,解:(1)出钢量=(3200×6+20×6+120+150)×0.9872=19339.25(kg)(2)(k。。
Fe、C、Mn的氧化损失量在氧化法和返吹法中基本相似。在一般情况下,Al、Ti、Si元素在氧化法中几乎全部氧化掉,P只能大部分氧化,但这些元素在返吹法中,因不使用矿石助熔,氧化损失略少些,而在不氧化法中为少。在冶炼高合金钢时,如炉料的配Si量大于1.0%,Si的氧化损失量约为50%~70%。铁的氧化损失通常为2%~6%。废钢质量越差,熔化时间越长,吹氧强度越大,铁的氧化损失也越大。碳的氧化损失量一般为0.60%,但不用氧时碳的损失不太大。而用氧时,碳的变化与钢液中的碳含量、吹氧强度有关。当炉料中的配碳量小于0.30%时,碳的氧化损失不大,并可为电极增碳所弥补;配碳大于0.30%时,碳的氧化损失要多。