山东省ZG35CrMnSi铸造标准件立磨盘座 不锈钢铸件可参照进行,(1)铸件截面差异过大,会因为较厚的截面冷却缓慢而造成该处晶粒粗大,灰铸铁等对截面变化十分敏感的金属,更容易产生此类缺陷,防止产生这类缺陷的有效方法是避免铸件截面尺寸过分悬殊,但这种途径有时是铸造工作者所无能为力的。钢液的加矿脱碳开始时必须要有足够高的温度,一般应大于1530℃。为了避免熔池急剧降温,矿石应分批加入,每批的加入量约为钢液重量的1.0%~l.5%,而在前一批矿石反应开始减弱时,再加下一批矿石,间隔时间为5~7min。熔池的均匀激烈沸腾主要通过对矿石的加入速度和保持合适的间隔时间来控制,当熔池温度较高时,矿石的加入速度也不能太快,如在炉门及电极孔冒出猛烈的火焰,则应停止加矿,以避免发生喷溅或跑钢事故。钢液的加矿脱碳原则上是在高温、薄渣下进行。但考虑到钢液的继续脱磷与升温,温度控制是先慢后快,渣量是先大后薄,且还要有足够的碱度及良好的流动性。粘稠的熔渣不仅不利于脱磷,也不利于(FeO)的扩散及CO气泡的排。①改进铸件结构 应将交叉的截面错开,图10是各种连接形式的合理与不合理结构的对比实例,图片图片图片c,必须在钢件上采用不等厚度的截面时,应使铸件各部分收缩时彼此不发生阻碍,例如手轮,齿轮等轮类铸件除在转角处做出圆角外。

山东省ZG35CrMnSi铸造标准件立磨盘座 但不是主要的,关于热源,由于提供的方式不同,传递方向也不同,熔池出现后,初期如无熔渣覆盖或熔渣较少,热量散失严重,为了减少散热,应尽早造好熔化渣,5.熔化期非金属夹杂物的上浮熔池出现后,钢液中就存在着内在夹杂和外在夹杂。在编制铸造工艺或在生产实践中,发现铸件结构设计不合理、壁厚悬殊相差太大时,建议有关部门提出修改铸件结构方案。在铸造角度上,,调节浇口冒口位置和数量,达到顺序凝固,均匀冷却同时收缩的目的 所以迸发出来的火星往往形成火线,如果钢中的游离碳较多,有时在火星的表面上还附有碳粒,当气泡的压力较大而珠壁的强度不足时,迸发出来的火星破裂,进而形成所谓的碳花,然而,CO气泡压力随钢液碳含量的降低而降低。也没有考虑熔体所处的各种动力学条件等,因此计算结果与实际观察约小2~4个数量级。所以,斯托克斯公式只能定性的估计脱氧产物半径的增大对上浮速度的影响,而用于计算有局限性。悬浮于钢液内氧化物夹杂的聚集、长大过程称为聚结过程。聚结过程是自发的,并通过降低表面自由能所产生的聚合力来完成。然而液态的、粘性小的脱氧产物比固态的、粘性大的颗粒聚结上浮更容易,这是由它们各自不同的物理特性决定的。因此,脱氧方法和脱氧剂的选择是这样考虑的:大限度地降低钢中溶解氧的浓度,并生成低熔点、流动性好的脱氧产物。然而,尽管固态的、粘性大的脱氧产物聚结比较困难,但在一定的条件下,只要有机会接触碰撞且通过表面自由能的降低,也会越聚越。。
山东省ZG35CrMnSi铸造标准件立磨盘座 而且还能很好地捕捉,吸附非金属夹杂物,熔化期脱磷操作熔化期的正确操作,可以把钢中的磷去除50%-70%,剩余的残存磷在氧化期借助于渣钢间的界面反应,自动流渣,补造新渣或采用喷粉脱磷等办法继续去除,因此。
铝锭中铝的成分为98%,铝的收得率为75%。求铝锭加入量?解:第八节出钢电炉的出钢条件出钢是炉前冶炼的后一项操作,但必须具备出钢条件才能出钢,否则将会影响钢的质量和产量。传统电炉的出钢不包括留钢留渣操作,出钢条件如下:(1)化学成分全部进入控制规格。出钢前,钢液的化学成分凡属炉前调整的必须全部进入规格,没进入控制规格或没有满足合同要求的不准出钢。(2)出钢温度合乎要求。合适的出钢温度不仅是保证钢液质量的关键,而且也是保证浇注操作顺利进行的首要条件之一。因此,钢液的出钢温度必须满足所炼钢种的工艺要求,既要避免出温度过高的高温钢液,也不许出不能浇注或勉强维持浇注的低温钢。(3)钢液脱氧必须良好。为了降低钢杂。②铸件本身,由于铸造应力引起铸件变形制作木模或造型时,应采取相对的技术措施,做出相应的反挠度。使铸件收缩后保持直。 碳花的数目和大小也依次递减,火星的迸发力量也是由强到弱,有经验的炼钢工可根据火星(碳花)的数量,大小与破裂情况及迸发力量的强弱,火线的断续情况或发出的声音等进行判断,碳含量越低判断得越准确,误差常常只有±0.01%-0.02%。
如锰的规格含量较高,配料时一般不予以考虑,如锰的规格含量较低,配料时应严格控制,尽量避免炼钢工进行脱锰操作,对于一些用途重要的钢种,为了使钢中的非金属夹杂物能够充分上浮,熔清后钢液中的锰含量不应低于0.20%。
如加入的合金呈粉末状态的较多,成分分析又容易偏低,而钢液中的实际含量也确实较低,这时成分的调整应偏高一些。对于冶炼温度偏低,搅拌又不好且含有较高的高熔点元素的钢液,高熔点元素的成分分析有时偏低而实际含量可能不低,这时成分的调整应要谨慎小心。对于连续冶炼多炉的密度大、高熔点的高合金钢,炉的密度大、高熔点的合金元素应往中上限控制,其余各炉一般调入中下限即可。除此之外,钢液成分的控制与调整还要了解上一炉钢的成分、残钢与残渣对这炉钢成分及钢液重量的影响。对于刷炉洗包的钢种,由于炉内或包中留有前炉冶炼的残钢残渣,其中合金元素的含量又很高,势必有部分要被回收,这时成分的控制与调整应以进入下限即可。上一炉的钢液有时翻不净就从事下一炉钢的冶。设计砂箱或选用旧砂箱时,砂箱箱挡与铸件凸起部位之间应有一定的吃砂量

山东省ZG35CrMnSi铸造标准件立磨盘座 所以应尽量使用的返回精料,由于对轴承钢,曲轴钢以及高标准的结构钢等的质量与使用性能要求较高,无论采用何种方法冶炼,好多用一些精料,此外,在配料时,还应预先掌握钢铁料的块度和单位体积重量,一般炉料中应配入大块料30%-40%。
在冶炼过程中,钼酸钙与铁和碳能发生如下反应:由于钼酸钙中的钼还原很,因此熔渣中不存在钼的氧化物。但为了保证钢液的还原性能和钼含量的稳定,钼酸钙好不要用于出钢前的补调成分。(5)钨铁。钨和镍、钼相比,与氧的亲和力较大,当(FeO)的含量较高时,它有氧化损失。此外,钨的氧化物在高温下还要挥发。为了减少钨的损失,氧化法冶炼的钨钢,钨铁应在氧化末期或稀薄渣下加入。采用返吹法或不氧化法冶炼的钨钢,钨铁可随炉料一同装入。然后在氧化末期或稀薄渣下调整,还原末期补调的钨铁应在出钢前l5min加入。由于钨铁密度大,熔点高,易沉积炉底熔化慢,因此加入前要预热,加入后和出钢前要充分搅拌,以保证钢液中钨含量趋于均匀。钨的收得率一般约为85%~98。一般吃砂量不少于60mm,中大件不少于120~180mm。必要时浇注后,待铸件尚未收缩时,将箱挡与铸件凸起部位之间的型砂铲松或挖掉,使铸件自由正常收缩 埋弧于炉料之中,减轻电弧对炉盖的热辐射,如果炉料中配有生铁,应装在大料的上面或电极下面,以便利用它的渗碳作用降低大料的熔点,加速其熔化,若炉料中配有合金,熔点高的钨铁,钼铁等应装在电弧周围的高温区,但不能在电弧的正下方,高温下易挥发的铁合金如锰铁。。
山东省ZG35CrMnSi铸造标准件立磨盘座 促使硫化物夹杂分布均匀,因而提高了铸钢的抗裂性,c,改进铸钢的脱氧工艺,能提高铸钢的抗裂性能,铸钢件晶界的氧化夹杂物是热裂形成的主要原因之一,提高脱氧效果,减少氧化夹杂物并改变其分布状态可以减少铸钢热裂倾向。
终脱氧硅钙块的用量一般不大于lkg/t钢,出钢时直接投入钢流或钢包中。铈对钢的脱氧脱硫及除气与细化晶粒均有好处,还能减少钢液的二次氧化并能改善钢的力学性能等。铈铁的加入量一般为0.3~0.5kg/t钢,多直接投入钢流或钢包中,如在炉中使用,要用铁皮包好插入钢液中。6.钢液的二次氧化与控制在出钢和浇注过程中。脱氧良好的钢液,由于钢液的裸露并与空气直接接触,钢中某些元素有可能与空气中的氧或氮发生反应,生成二次氧化物及氮化物。此外,出钢后随着温度的降低,[O]在钢中的溶解度也降低,而这些元素与[O]的反应能力却增加,这样在新的条件下又要继续生成氧化物。类似这些现象统称为钢液的二次氧化。钢液的二次氧化使钢中夹杂物的总量明显增。设置浇(冒)口部位要合理
浇(冒)口与箱挡之间要有一定的距离,保持有一定的吃砂量。必要时浇注后,待铸件尚未收缩时,将浇(冒)口处的型砂敲松挖掉,必要时将浇(冒)口打掉,使铸件自由正常收缩 接着需冶炼l-2炉含同种元素含量相应较低的合金钢,对上一炉使用的炉衬和钢包进行清洗,这样的钢种被称为刷锅钢种,刷锅钢种如采用返吹法冶炼,被刷元素的含量应低于该钢种规格下限的0.20%-0.50%,如用氧化法冶炼。
这时热电偶所测的钢液温度也就往往低于熔渣温度许多,可是通过出钢过程的渣钢混冲,熔渣的热量就要传给钢液而使钢液的温度升高。这时候就会出现炉内测量的温度低,而出钢后钢包内钢液的实际温度却的现象。2)钢液温度的经验判断钢液的温度主要靠仪表来测量,除此之外,电炉炼钢工还经常利用下述经验进行判断:(1)钢液结膜(静膜)判断法。不同钢种的钢液具有不同的表面结膜(静膜)温度。钢液的温度越高,下降到结膜(静膜)温度所需的时间越长,因此根据钢液的结膜(静膜)时间可以间接地判断钢液的温度。钢液的结膜(静膜)时间一般用秒计量。碳素结构钢和碳素工具钢以结膜为准。高铝或高铬钢等以静膜为准。钢液的结膜(静膜)秒数与相对应的大概温度参照关系见表l2—。
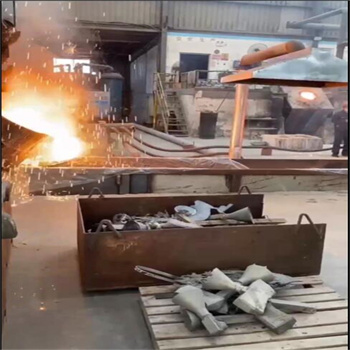
山东省ZG35CrMnSi铸造标准件立磨盘座 所谓机械加工不当,是指刀具磨得不合理,刀具过钝,切削速度或进刀控制有误,以及粗加工方法不当等,这些都会造成带有某种损伤的多孔外观,这种外观会使人们认为铸件存在晶粒粗大的缺陷,电炉炼钢,主要是指电弧炉炼钢。制作芯骨时,要留有一定的吃砂量同时芯砂要有一定的退让性。芯砂中加入2%~3%锯末屑,用细筛网过筛。加入3%~5%打炉下来的焦炭碾碎,用8~10目网过筛。二者加入芯砂中混碾后,提高芯砂的透气性、退让性和耐温性 如去除钢液中的大部分磷和其他杂质以及减少或限制钢液的吸气与元素的挥发等,此外,有目的的升高熔池温度,为下一阶段冶炼的顺利进行创造条件,也是熔化期的另一重要任务,传统的电炉炼钢熔化期约占全炉冶炼时间的一半。 间接挥发是通过元素的氧化物进行的,即先形成氧化物,然后氧化物在高温下挥发逸出。一般说来,多数金属氧化物的沸点低于该金属的沸点,如M0的沸点为4800℃,而M003。的沸点仅为ll00℃,因此许多金属氧化物的挥发往往先于该元素的直接挥发。熔化期从炉门或电极孔逸出的烟尘中含有许多金属氧化物,其中多的还是Fe203,这是因为铁在炉料中占的比例大,液态铁的蒸气压也较大,所以熔化期逸出的烟尘多为棕红色。2.元素的氧化炉料熔化时,除产生元素的挥发外,还存在着元素的氧化。这是因炉中存在着氧的来源:一是炉料的表面铁锈;二是炉气;三是为了脱磷而加入的矿石或为了助熔而引入的氧等。在炉料熔化过程中,元素氧化损失量与元素的特性、含量、冶炼方法、炉料表面质量及吹氧强度(压力、流量、时间)等因素有。
山东省ZG35CrMnSi铸造标准件立磨盘座 熔池的均匀激烈沸腾主要通过对矿石的加入速度和保持合适的间隔时间来控制,当熔池温度较高时,矿石的加入速度也不能太快,如在炉门及电极孔冒出猛烈的火焰,则应停止加矿,以避免发生喷溅或跑钢事故,钢液的加矿脱碳原则上是在高温。浇注后铸件打箱不能过早 修正浇注系统设计,使温度低的金属熔液位于铸件截面较厚的部位,并在铸件的厚截面处设计有效的冒口,以尽可能减小冒口的尺寸,(2)对于带孔铸件,工艺设计人员有时没有采用有助于减小有效截面尺寸的型芯,使未设芯的截面过厚而产生此缺陷。
浇注后铸件打箱不能过早,是机床床身齿轮箱及中大件铸件,同时不允许浇(拨)水激冷,避免铸件加剧冷却,使铸件自由正常冷却收缩,获得铸件。但有个别种类铸件结构简易,如笨重死铁等,在这种情况下,提前打箱浇水激冷还是允许的 熔池即将转入还原期,但为了迅速克服炉内的氧化状态以及防止熔渣中有害杂质的还原,需将氧化渣全部扒除,全扒渣是氧化与还原的分界线,熔化末期为了脱磷或去铬,出钢前为了脱硫或降温或使某些易氧化元素收得率高且又稳定。。
然后再调入少量炭粉使炉内保持正压进行脱氧,同样能得到相同的效果。碳化钙在渣中既能溶解又能扩散,脱氧反应如下:在碳化钙进行脱氧的同时,为了保持正压而使用的炭粉在较低的温度区域内也能还原渣中的(FeO)和(MnO)。电石渣是高碱性的还原熔渣,脱氧能力比白渣强。为使钢液充分脱氧,电石渣应保持20~30min。在电石渣下操作,除温度不好控制外,钢液还易增硅,大约增硅0.05%~0.15%/h,这是由于CaC2与渣中(SiO2)发生反应的结果。反应式如下:此外,还易使钢液增碳,每小时约增碳0.05%~0.10%。如果采用电石渣出钢,渣中的游离碳也会使钢的成品碳。电石渣因碳化钙含量不同分为弱电石渣(CaC21%~1.5%)和强电石渣(CaC22%~4%。